Fiber Bragg grating (FBG) sensors
B-SENS designs and develops fully-customizable FBG sensing solutions that can yield quasi-distributed measurements and communicate the processed data to the end user.

These developments encompass the production of the FBG sensors (1), their functional coating, protection or packaging (2) and the data acquisition system (3).
1. FBG
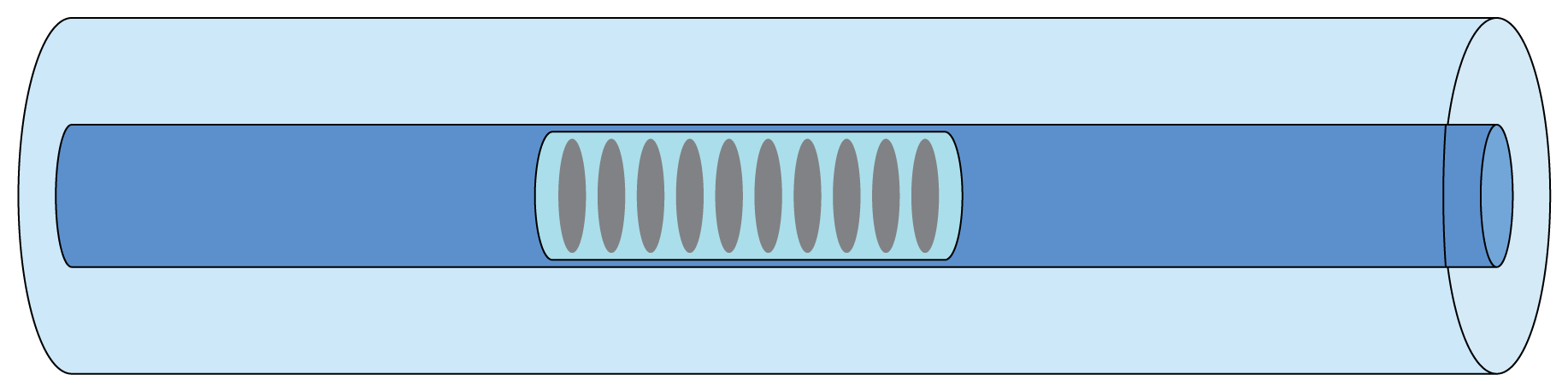
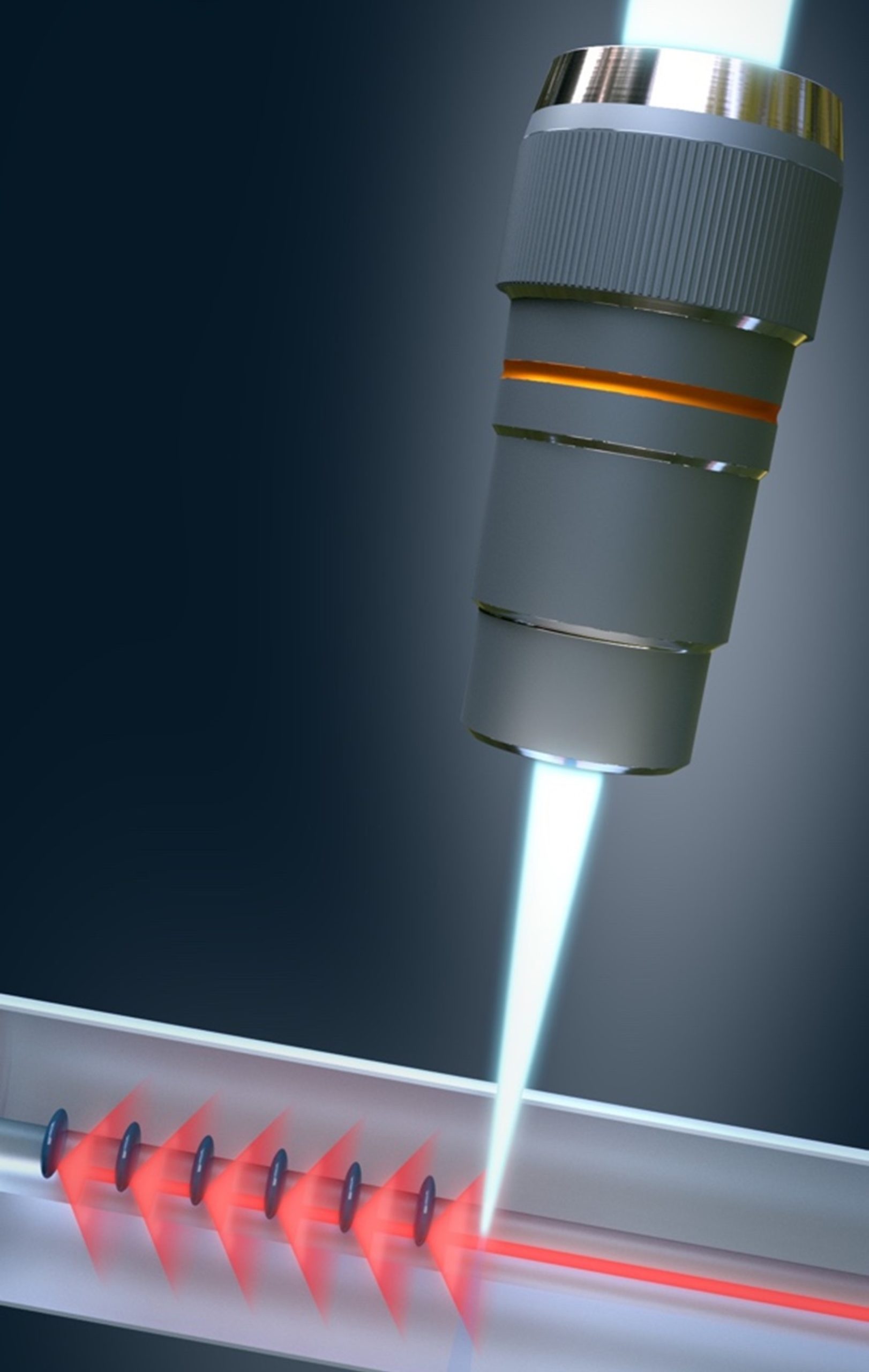
FBGs are produced in telecommunication-grade optical fibers (outer diameter of 250 µm) by local laser irradiation transversely to the optical fiber axis.
They are usually short in length (<1 cm) and act as bandpass filters in reflection around the so-called Bragg wavelength.
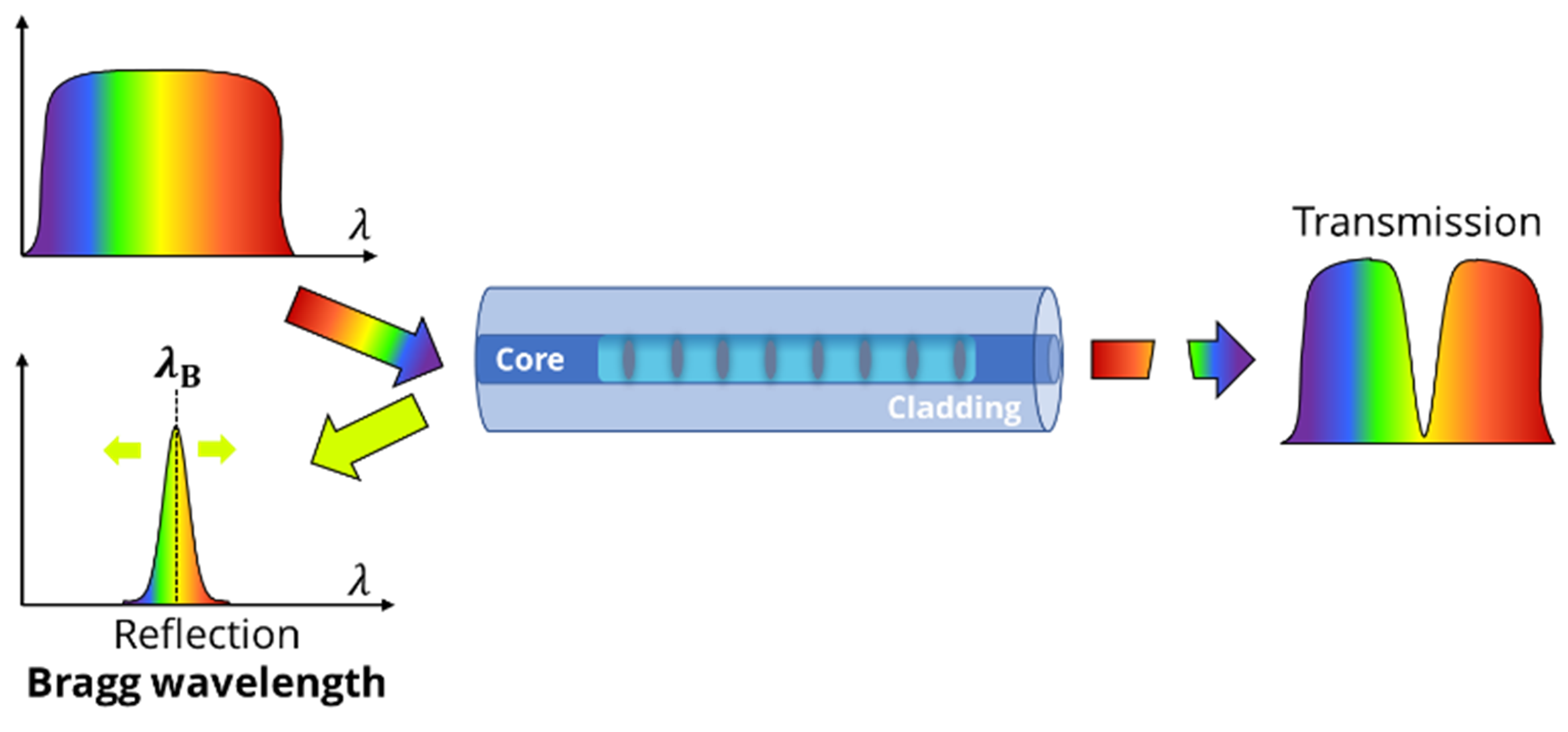
They are inherently sensitive to temperature changes and axial strain, which induces a shift of their Bragg wavelength. Tracking this shift allows to determine the actual temperature or strain value after calibration.
Nominally, they can reflect the temperature value at +/- 0.1 °C and the strain value at +/- 1µε.
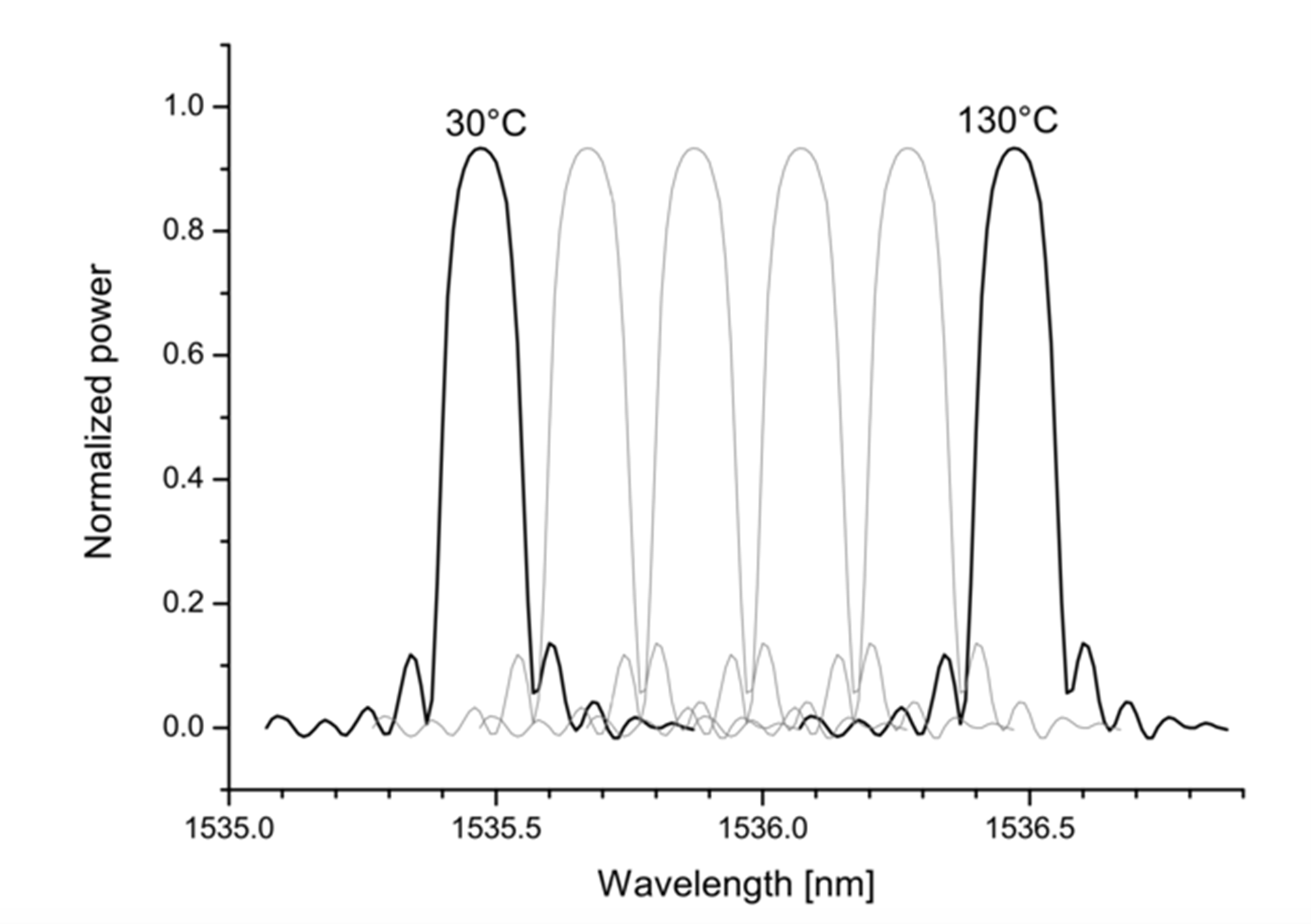
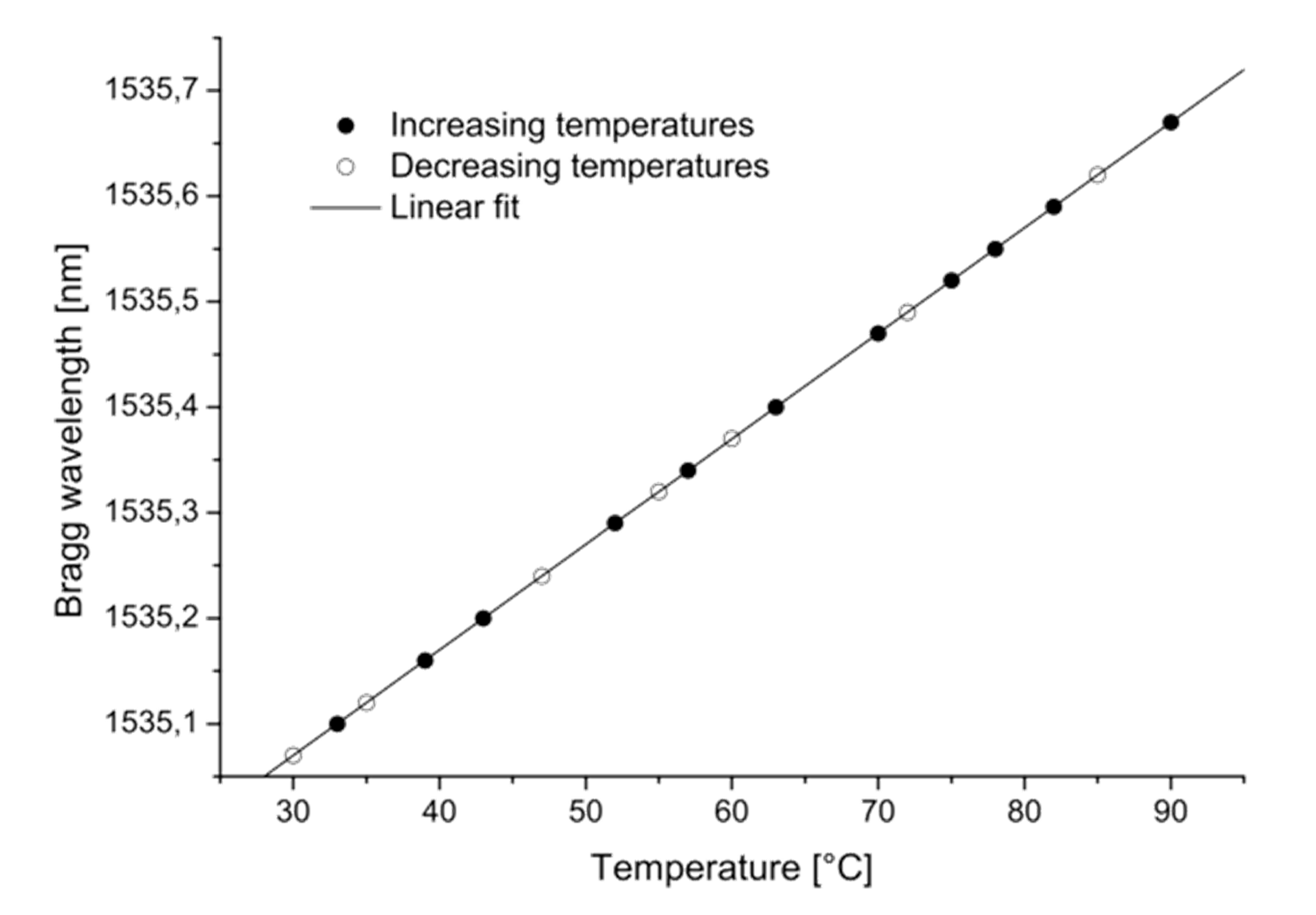
This innovative technology brings the following advantages…
2. Coating/Protection/Packaging
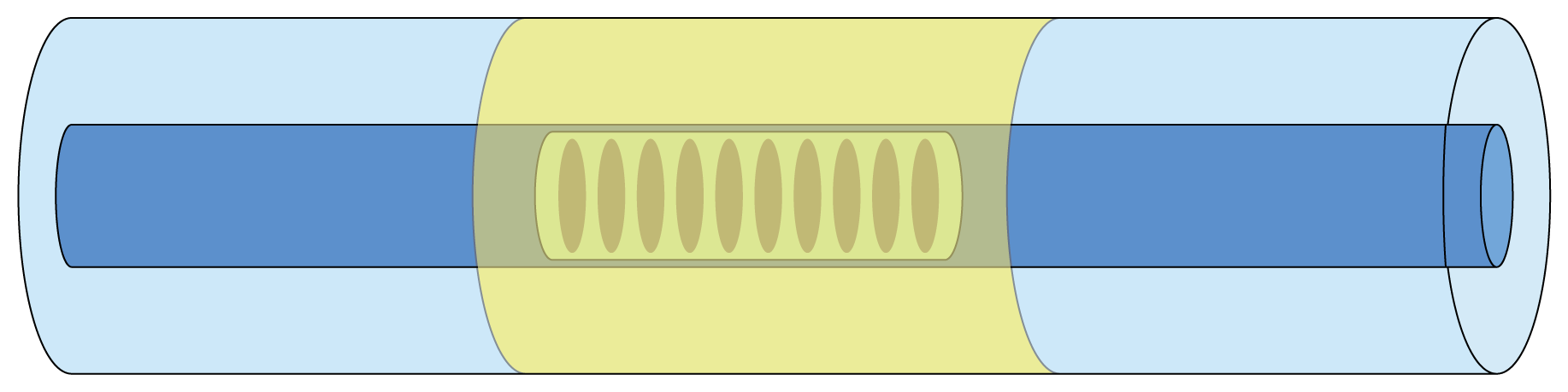
Specific coatings can be applied to the optical fiber surface at the FBG location to widen the sensing modalities. We have solutions to enable hydrogen sensing, early fire detection
and we can develop other specific coatings.
Our expertise in this field is quite unique and multifold. We make use of organic, inorganic & metal coatings. Their synthesis is ensured by various physical/chemical processes.
Depending on the target application, a specific protection and/or packaging can be applied around the FBG. Metal layers, glass, aluminum, ceramic or Teflon tubing are some prominent examples.
3. Data acquisition system
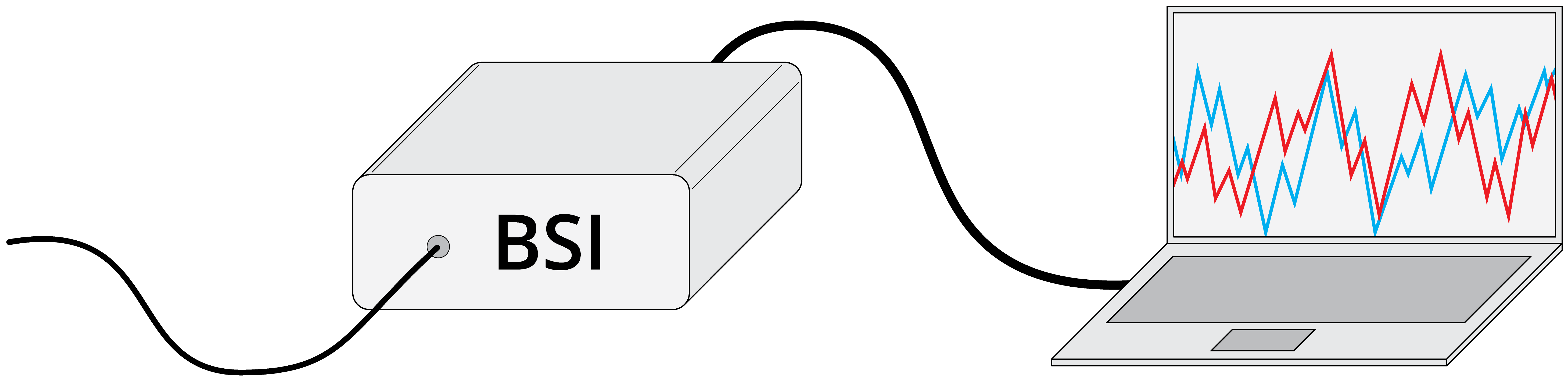
The read-out unit is the measurement device that launches light within the optical fiber cable and collect the FBG amplitude spectrum. While optical fibers can be considered the nervous system of the sensing solution, the read-out device
is its core.
We have developed two complementary devices families:
Both solutions are very competitive in terms of performance and cost. They are provided with a stand-alone and user-friendly interface (either in Labview or Python), called B-SOFT, that processes and communicates the data. It can be adapted
depending on customer’s requirements.